Silicone Molding/Urethane Casting
At a Glance
Applications
Lead Time
Materials
Finishing Options
About the Process
Silicone Molding (also known as RTV molding, Urethane Casting, and Vacuum Casting) is a fabrication method that uses silicone molds to produce production-quality parts, without the high costs and lead times of steel or aluminum tooling.
It is known for its fast production of high-quality prototypes or end-use products.
Silicone Molding production consists of three main steps:
1. Build a master pattern using 3D printing or CNC machining.
2. Build the mold by pouring platinum silicone around master.
3. Pour liquid polyurethane resin into mold, create polyurethane casting under vacuum.
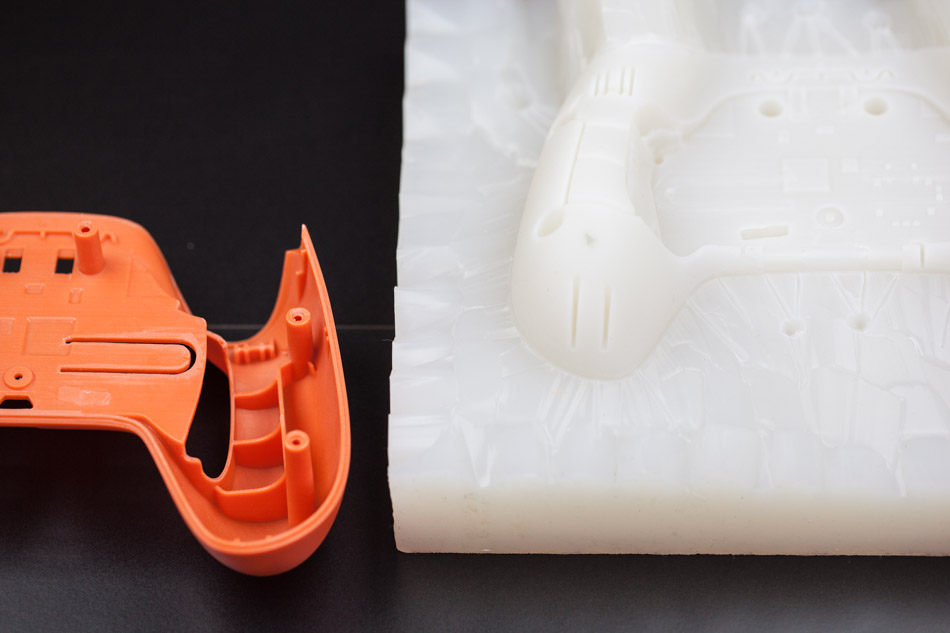
Why choose Silicone Molding
Silicone molding results in high-quality parts comparable to injection-molded components. This makes vacuum casted models especially suitable for fit and function testing, marketing purposes or a series of final parts in limited quantities. Vacuum Casting also lends itself well to a variety of finishing degrees, and we can match the finish you need for your parts.
Choose Silicone Molding for:
Choose a different process for:
Materials
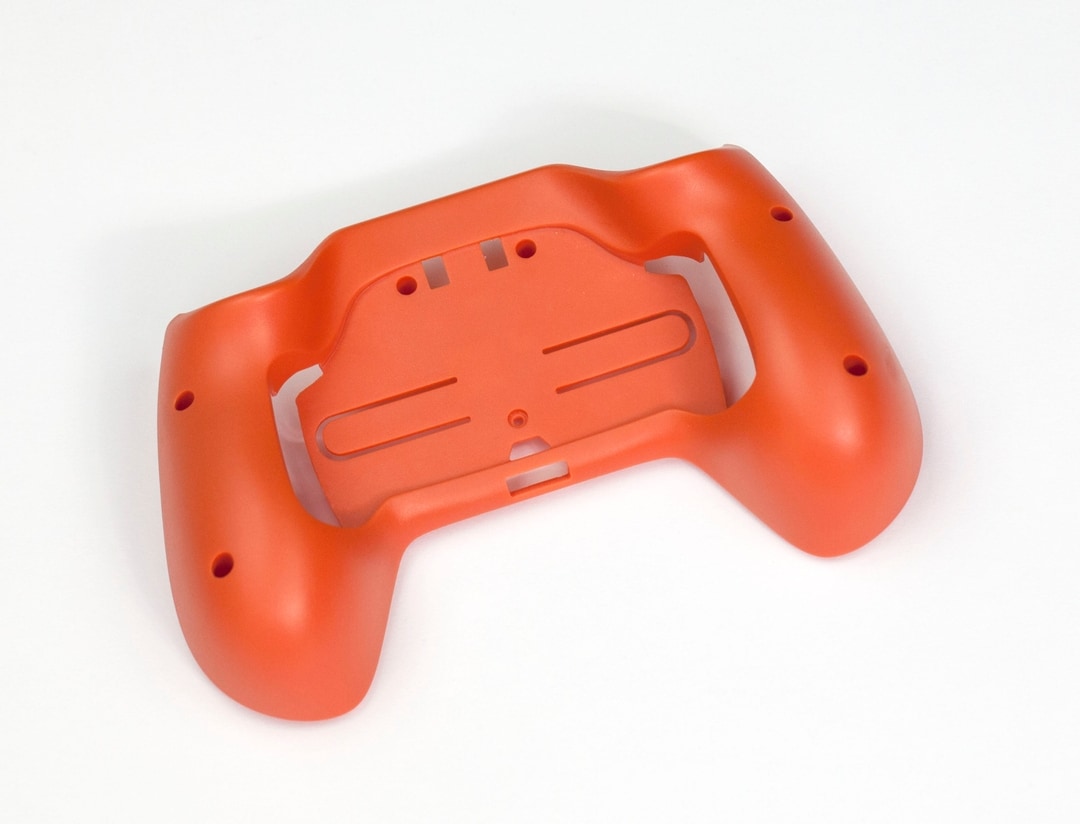
ABS-like
A general-purpose opaque material that simulates ABS
thermoplastic. Good for most hardware product enclosures,
mechanical and functional parts.
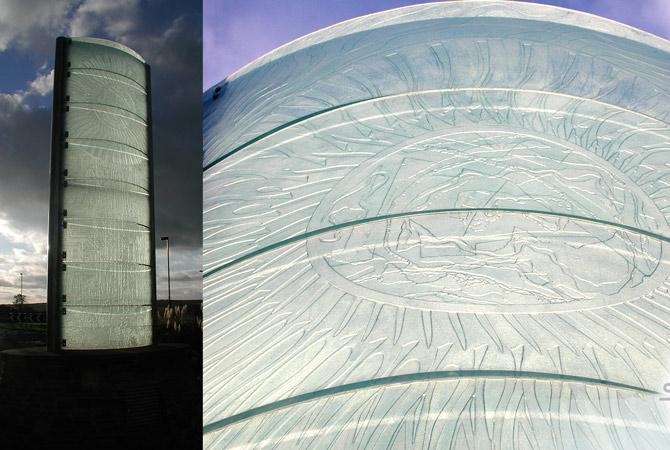
Acrylic-like
A stiff, transparent material for simulating acrylic
(PMMA). Good for see-through applications such
as light guides.
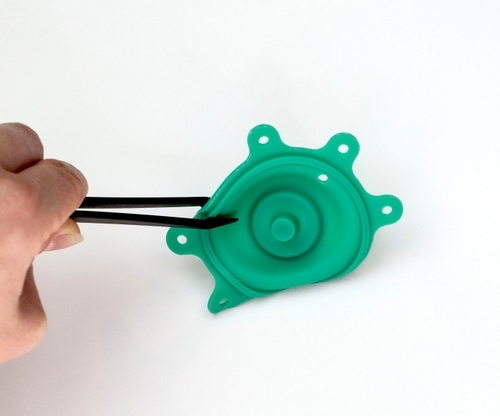
Opaque Rubber
Simulates all kinds of rubber-like materials such as
TPE, TPU, and silicone rubber. Great for wearables,
gaskets, and overmolds. Available from Shore 20A
to Shore 90A in 10A increments.
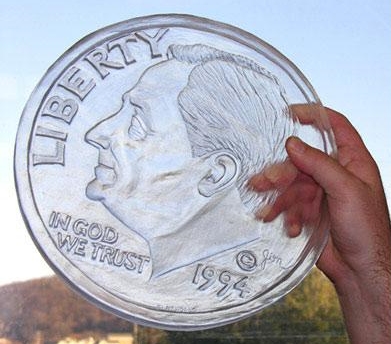
Clear Rubber
Simulates all kinds of rubber-like materials such as
TPE, TPU, and silicone rubber. Great for wearables,
gaskets, and overmolds. Available from Shore 20A
to Shore 90A in 10A increments.
Colors and Finishing Options
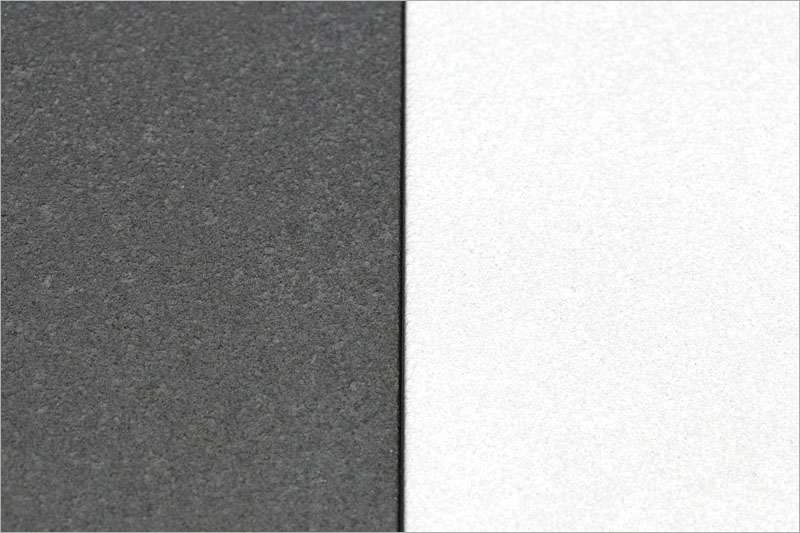
Standard
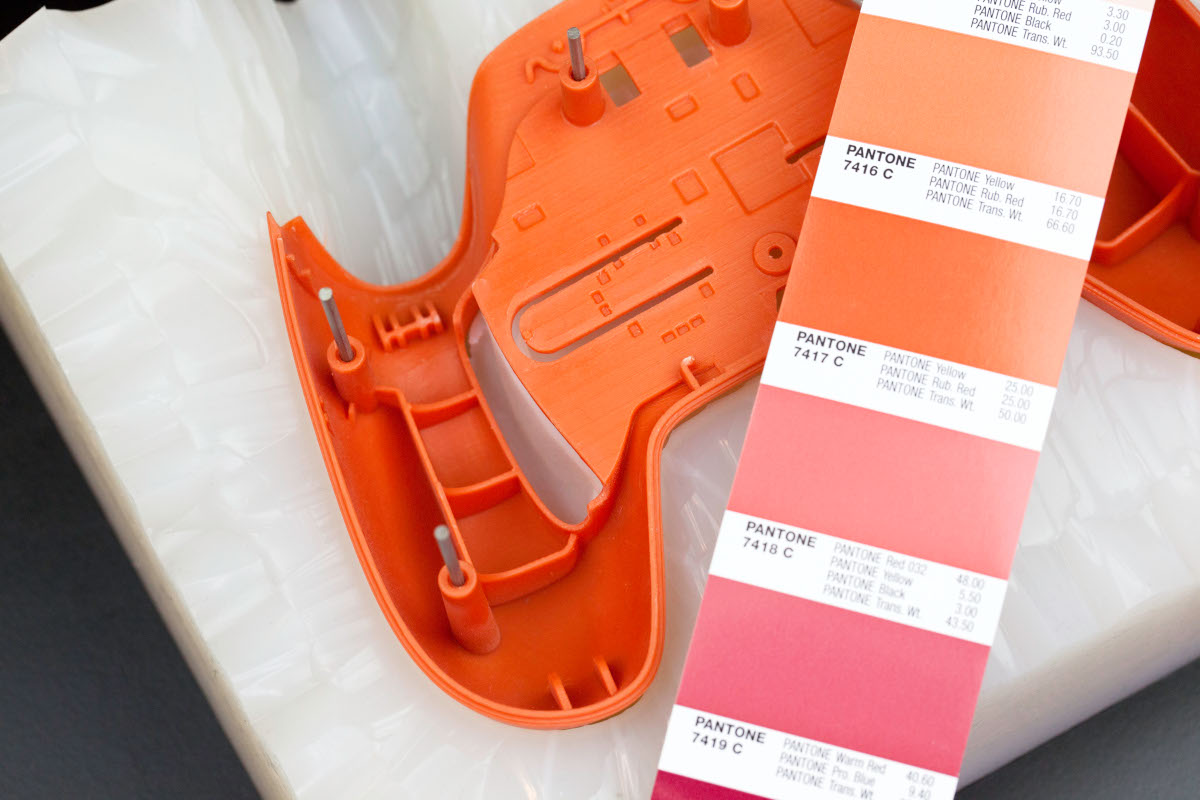
Precise Color Match
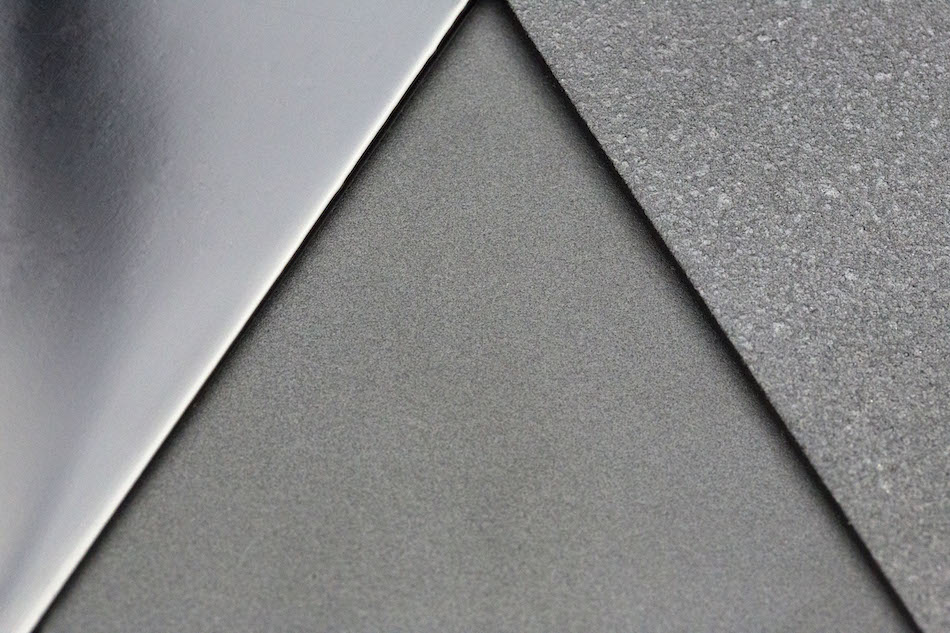